Planetary gears are very popular as power transmission and extensively used in different industrial fields like automobiles, helicopters, aircraft engines, heavy machinery, and a variety of other applications to perform speed reduction due to several advantages over conventional parallel shaft gear systems. The advantages include compactness, high torque to weight ratios, reduced radial bending loads. Many researchers have worked to optimize the radial size of the planetary gear box.
The planetary gear boxes have some advantages over normal gear boxes. Planetary gear boxes are more accurate and high precision due to their compactness. Planetary gear boxes have high efficiency and less power loss. High precision 75W – 2000W DC planetary gear motor refers to a combination of a three-phase brushless motor and a planetary gearbox. Due to these features, multi-stage gear boxes are used for high-power transmitting applications. It is a popular type of gear motor.
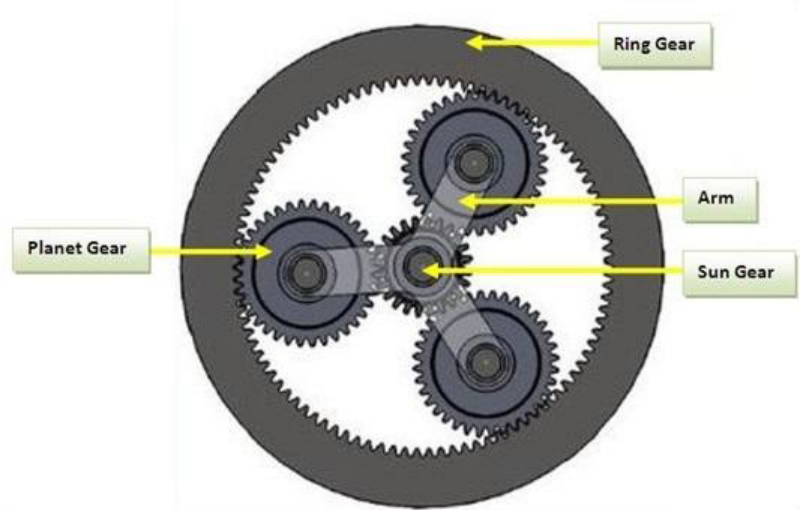
It shows the basic layout of the planetary gear set which consists of four different elements that produce a wide range of speed ratios in a compact layout. These elements are
- Sun gear, an externally toothed ring gear co-axial with the gear train
- Annulus, an internally toothed ring gear coaxial with the gear train
- Planets, externally toothed gears that mesh with the sun and annulus, and
- Planet Carrier, a support structure for planets, co-axial with the train. Planetary gear system as shown in it is typically used to perform speed reduction due to several advantages over conventional parallel shaft gear systems. Planetary gears are also used to obtain high power density, a large reduction in small volume, pure torsional reactions and multiple shafting. Another advantage of the planetary gearbox arrangement is load distribution.
The more the planets in the system, the greater load ability and the higher the torque density. The PGT arrangement also creates greater stability due to the even distribution of mass and increased rotational stiffness. In today’s scenario, there is the need for light weight and compact gearbox design with high load carrying capacity and compact in size. So many researchers have worked to the size of the planetary gearbox.
- Studied the robust model stiffness of cylindrical gears & pinions. He studied that reduced rim and web thickness results in smaller mesh stiffness Studies conducted by D.I.Syed
- To optimize the design of the planetary gear trains based on the load analysis. One more researcher B-R.Hohn.
- Worked on lowering the weight of the planetary gear box. More the load factor required, more mesh load necessary; this will result in complexity in the assembly of the planets with lower number of teeth.N..Marjanovic
- Studied practical approach to the optimization of planetary gear trains with spur gears. In his study, he presented the selection of optimal gear trains and also a selection of optimal position for shaft axes of gears trains with “spur gears”. In this, the volume of the planetary gear trains with “spur gears” is drastically reduced by 23% J. Stefanović
- Conducted study of planetary gear box optimization. He formulated objective function with optimization variables considering face width, gear modules and optimization function as volume, mass and manufacturing cost, efficiency. The study conducted by O. Bunga al. [6] in his study on mass optimization of the design of two-stage coaxial high speed reducer with GA (Genetic Algorithm) compared in the conventional design of gear reduction with optimized design by GA.
He studied about the compromise between the service life and mass was presented & they concluded and understood that the required service life needs to be sacrificed with some percentage (75%) for a 2.5 kg saving (roughly 7%). U. Kissling also did a study on the same line on an optimization procedure used for a complete planetary gear box with weight, cost, torque and dimensional restriction. After an exhaustive literature survey, it is seen that a large amount of effort has been put to optimize the radial size of the gear box. It is seen that the efforts for reducing the axial length of the gear box keeping the load-carrying capacity the same gives very good vertical space reduction in existing gear for CNC bending machine tools and hence we have decided to conduct the research in this area.