A gear is a toothed wheel that engages another toothed mechanism to change speed or the direction of transmitted motion. Gearmotors will introduce the types, characteristics and applications of gear.
Here is a brief list of the common forms.
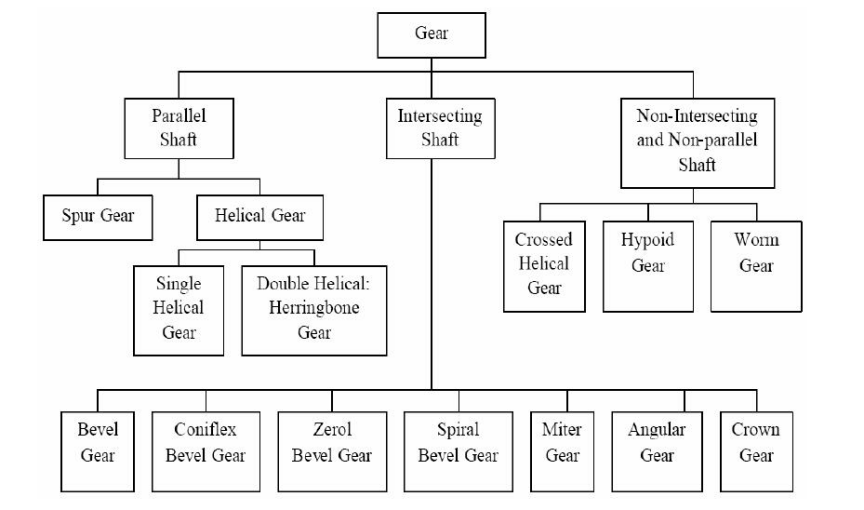
Spur Gears
Spur gears are used to transmit power between two parallel shafts. The teeth on these gears are cut straight and are parallel to the shafts to which they are attached.
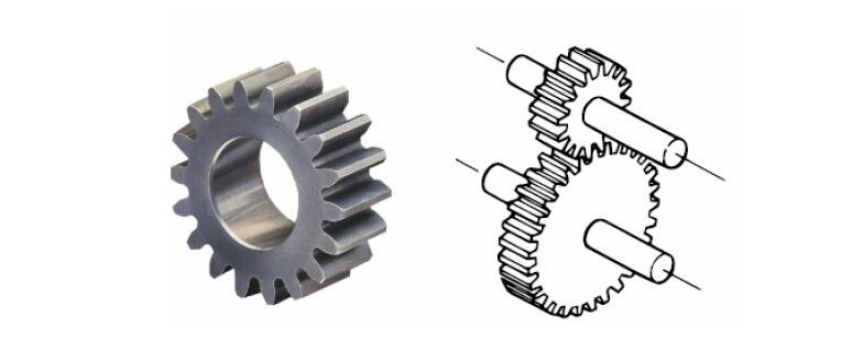
Characteristics:
- Simplest and most economical type of gear to manufacture.
- Speed ratios of up to 8 (in extreme cases up to 20) for one step (single reduction) design; up to 45 for two step design; and up to 200 for three-step design.
Limitations:
- Not suitable when a direction change between the two shafts is required.
- Produce noise because the contact occurs over the full face width of the mating teeth instantaneously.
Helical Gears
Helical gears resemble spur gears, but the teeth are cut at an angle rather than parallel to the shaft axis like on spur gears. The angle that the helical gear tooth is on is referred to as the helix angle. The angle of the helix depends upon the condition of the shaft design and the relative position of the shafts. To ensure that the gears run smoothly, the helix angle should be such that one end of the gear tooth remains in contact until the opposite end of the following gear tooth has found a contact. For parallel shafts, the helix angle should not exceed 20 degrees to avoid the excessive-end thrust.
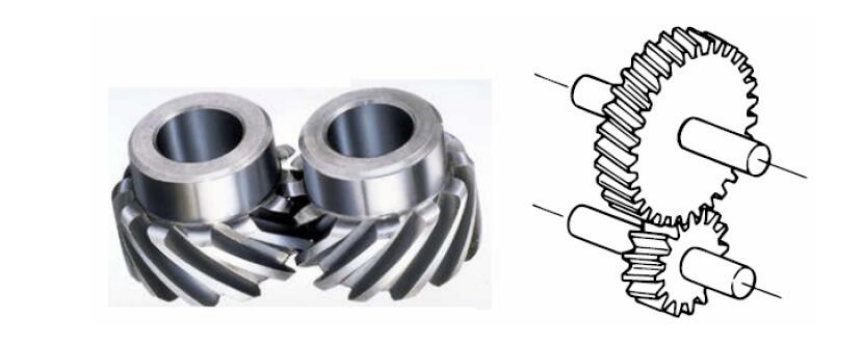
Characteristics:
The longer teeth cause helical gears to have the following differences from spur gears of the same size:
- Tooth strength is greater because the teeth are longer than the teeth of spur gear of equivalent pitch diameter.
- Can carry higher loads than can spur gears because of greater surface contact on the teeth.
- Can be used to connect parallel shafts as well as non-parallel, non-intersecting shafts.
- Quieter even at higher speed and are durable.
Limitations:
- Gears in mesh produce thrust forces in the axial directions.
- Expensive compared to spur gears.
Bevel Gears
A bevel gear is shaped like a section of a cone and primarily used to transfer power between intersecting shafts at right angles. The teeth of a bevel gear may be straight or spiral. The straight gear is preferred for peripheral speeds up to 1000 feet per minute; above that they tend to be noisy.
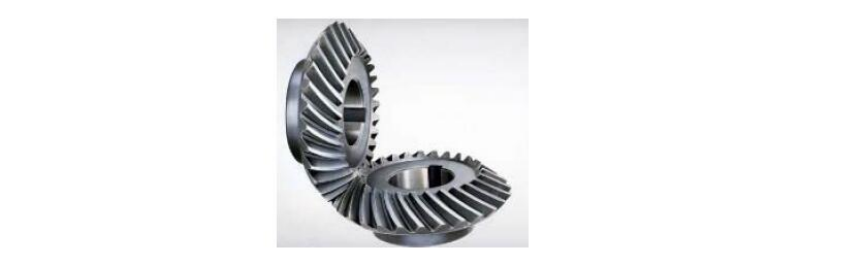
Characteristics:
- Designed for the efficient transmission of power and motion between intersecting shafts. A good example of bevel gears is seen as the main mechanism for a hand drill. As the handle of the drill is turned in a vertical direction, the bevel gears change the rotation of the chuck to a horizontal rotation.
- Permit a minor adjustment during assembly and allow for some displacement due to deflection under operating loads without concentrating the load on the end of the tooth.
Hypoid Gears
Hypoid gears are a modification of the spiral bevel gear with the axis offset. The distinguishing feature of hypoid gears is that the shafts of the pinion and ring gear may continue past each other, never having their axis intersecting.
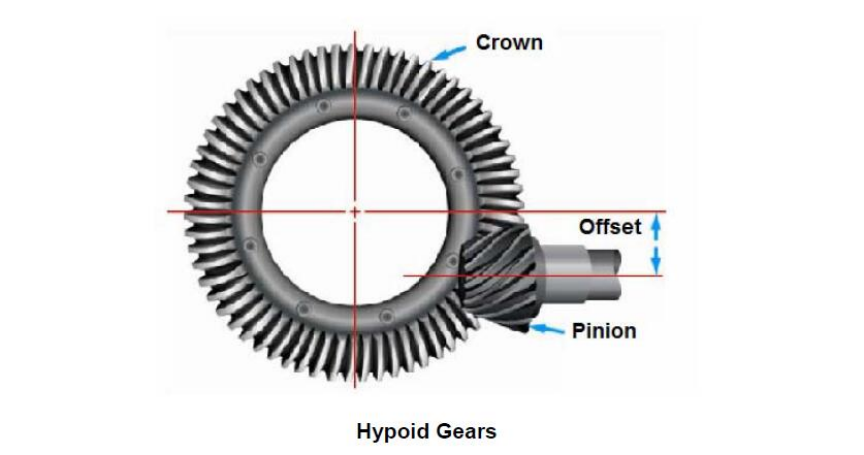
The major advantages of the hypoid gear design are that the pinion diameter is increased, and it is stronger than a corresponding bevel gear pinion. The increased diameter size of the pinion permits the use of comparatively high gear ratios and is extremely useful for non-intersecting shaft requirements such as automotive applications where the offset permits lowering of the drive shaft.
Worm Gears
Worm gears are used to transmit power between two shafts that are at right angles to each other and are non-intersecting. Worm gears are special gears that resemble screws, and can be used to drive spur gears or helical gears. Worm gearing is essentially a special form of helical gearing in which the teeth have line contact and the axes of the driving and driven shafts are usually at right angles and do not intersect.
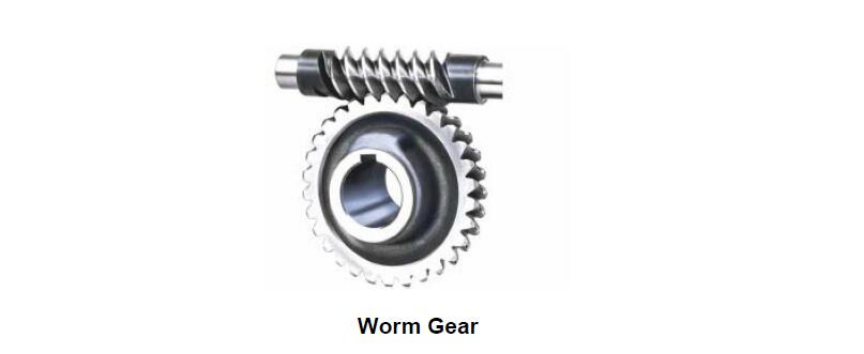
Characteristics:
- Meshes are self-locking. Worm gears have an interesting feature that no other gear set has: the worm can easily turn the gear, but the gear cannot turn the worm. This is because the angle on the worm is so shallow that when the gear tries to spin it, the friction between the gear and the worm holds the worm in place. This feature is useful for machines such as conveyor systems, in which the locking feature can act as a brake for the conveyor when the motor is not turning.
- Worm gear is always used as the input gear, i.e. the torque is applied to the input end of the worm shaft by a driven sprocket or electric motor.
- Best suited for applications where a great ratio reduction is required between the driving and driven shafts. It is common for worm gears to have reductions of 20:1, and even up to 300:1 or greater.
Limitations:
- Yield low efficiency because of high sliding velocities across the teeth, thereby causing high friction losses.
- When used in high torque applications, the friction causes the wear on the gear teeth and erosion of the restraining surface.
Internal Gears
Internal gears have their teeth cut parallel to their shafts like spur gears, but they are cut on the inside of the gear blank. The properties and teeth shape is similar to the external gears except that the internal gears have different addendum and dedendum values modified to prevent interference in internal meshes.
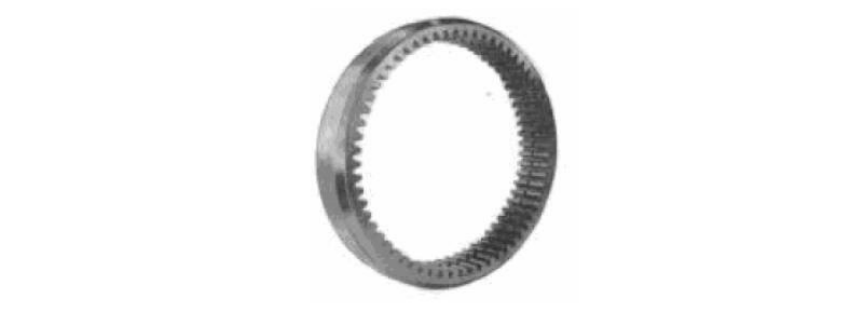
Characteristics:
- In the meshing of two external gears, rotation goes in the opposite direction. In the meshing of an internal gear with an external gear the rotation goes in the same direction.
- The meshing arrangement enables a greater load carrying capacity with improved safety (since meshing teeth are enclosed) compared to equivalent external gears.
- Shaft axes remain parallel and enable a compact reduction with rotation in the same sense. Internal gears are not widely available as standard.
- When they are used with the pinion, more teeth carry the load that is evenly distributed. The even distribution decreases the pressure intensity and increases the life of the gear.
- Allows compact design since the center distance is less than for external gears. Used in planetary gears to produce large reduction ratios.
- Provides good surface endurance due to a convex profile surface working against a concave surface.
Applications: Planetary gear drive of high reduction ratios, clutches, etc.
Limitations: Housing and bearing supports are more complicated because the external gear nests within the internal gear.